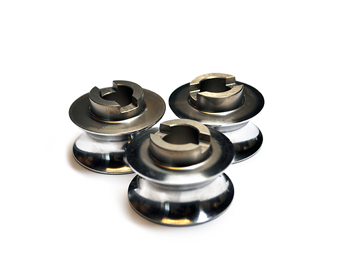
Burnishing rolls are manufactured holding extremely tight tolerances with polished surfaces to produce mirror-like finishes on your part.
When burnishing, the pressure generated by the rolls exceeds the yield point of the part surface at the point of contact, resulting in a slight deformation on the surface of the work piece.
Since most machined surfaces consist of a series of peaks and valleys of inconsistent height, the deformation created by roller burnishing displaces the material from the peaks into the valleys creating a mirror like finish with a tough, work-hardened and wear resistant surface.
There are many factors that need to be reviewed prior to quote, including material ductility and tensile strength, surface finish prior to and after burnishing rolls, and the diameter, length and shape of the part. Please contact our technical engineers and sales support to review your application.
How to Order Burnishing Rolls
When placing an order or requesting a quote for burnishing rolls, please have the following information available:
- Make and model of thread rolling attachment
- Style of thread roll (i.e. D-1, DR-1, C-1, etc.)
- Size and pitch of thread to be rolled, including dimensional tolerances if other than standard
- Length of thread on part
- Material to be rolled
- Is thread next to collet or cut off side
- Print of part to be rolled
Note:
- Special rolls may require a sample part or more detailed specifications.
- Some rolls require a special calculation to figure the work face on the roll.
knowledge base
learn more from our blog
AMERICAN STANDARD EXTERNAL TAPER PIPE THREADS
The United States uses ANSI’s American National Standard Pipe Thread Standards to regulate the formation
WHAT IS THREAD ROLLING?
Thread rolling is a metal forging process that forms threads into the mirror image of
TOP 10 THREAD ROLLING PROBLEMS
Most frequently used in the production of threaded rods, bolts, screws, and other metal fasteners, thread