Over our 60 years of providing thread rolling solutions, CJWinter has fielded several questions about the process — including dies, attachments, and other related tooling.
One of the most common questions we receive is: “How should I calculate thread rolling penetration rate?”
To help, we put together this quick three-step guide to determine the right penetration rate for your thread rolling application.
Step 1: Blank Diameter and Attachment Adjustments
Balancing blank diameter, pitch diameter, and major diameter is a sensitive process. With the proper pitch diameter achieved, you can begin narrowing down to the proper major diameter — important for calculating penetration rate.
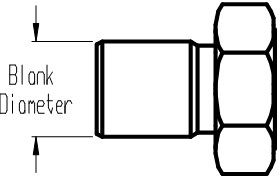
Achieving the correct major diameter usually requires increases in blank diameter. Because the major diameter increases proportionally to the blank diameter at a rate of three times, it is important that blank diameter be increased in the smallest possible increments.
In increasing blank diameter to achieve the proper major diameter, you are also increasing thread roll penetration resistance, essentially lowering penetration rate, also known as feed rate. A skewed penetration rate leads to a skewed pitch diameter. To correct the penetration rate, control the depth of penetration by making careful adjustments to the pitch diameter using the proper knob on the attachment.
Step 2: Determine Part Revolutions
The final application of your product, as well as its material, determines the ideal number of part revolutions in the thread.
In the thread rolling process, part revolutions directly relate to thread roll penetration. A method of penetration rate control, as it relates to part revolutions, is the control valve assembly — adjusting the flow control valve on the assembly’s “out” line will adjust penetration rate and part revolutions.
Because control valve assemblies have no clearly defined metrics by which to set them, penetration rate-expressing terms such as “inches per revolution” and “rolling time” are of estimation value only. To accurately and precisely determine and set a penetration rate, there is a simple five-step process:
- Determine recommended part revolutions using a reference chart such as the one below
- Determine the number of thread starts on the thread roll using the appropriate Reference Data Chart, of counting directly on thread rolls
- Divide recommended part revolutions by the number of starts; the result is the recommended compensator revolutions
- Observe the attachment compensator mechanism adjusting the collar while the machine is in operation
- Adjust the flow control valve to alter the penetration rate until the compensator makes the recommended number of revolutions
Thread Rolling | Brass Aluminum | Steel:Up to Rc 15 400 Series Stainless Steel | Steel:Up to Rc 15-32 300 Series Stainless Steel |
8-12 TPI Acme | 9-12 | 10-13 | Consult factor |
8-13 TPI UN or 3.0-2.0 MM | 8-11 | 9-12 | 10-14 |
14-20 TPI UN or 1.75-1.5 MM | 7-10 | 8-11 | 9-12 |
20-28 TPI UN or 1.25-1.0 MM | 6-9 | 7-10 | 8-11 |
29-Finer TPI UN or 0.8 MM-Finer | 6-7 | 6-8 | 6-9 |
Knurling | |||
12-17 TPI | 8-11 | 9-12 | 10-14 |
18-25 TPI or 64 DP | 7-10 | 8-11 | 9-12 |
26-35 TPI or 96 DP | 6-9 | 7-10 | 8-11 |
36-50 TPI or 128 DP | 5-8 | 6-9 | 7-10 |
51-Finer TPI or 160 DP | 5-7 | 5-8 | 6-8 |
As an example, a brass blank with a thread size of ¾-16 being machined with attachment 160-SA will have recommended part revolutions of 8 and 3 thread starts on a thread roll.
8 / 3 = 2.7
The penetration rate control valve should be adjusted to the point that the adjusting collar of the compensator mechanism makes between 2.5 and 3 revolutions.
Step 3: Remember the Formula
Penetration rate can also be calculated in terms of rolling time. The rolling time calculation is particularly useful in that it can be used to determine appropriate machine spindle speeds or estimated attachment cycle times. The rolling time formula is as follows:
Machine spindle speed (in RPM) / 60 = Rolling time (in seconds)
or
Recommended part revolutions / Machine spindle speed = Rolling time
Find Your Thread Roll
You can find more data about penetration rates and additional thread roll information in our Guide to Thread Rolling Solutions.

Go to the Thread Rolling Guide >>
Lib Pietrantoni
Lib has been with the Brinkman International Group, Inc. for the last 30 years. Currently the Director of Global Sales, Lib has held numerous positions in Engineering, Operations, Sales and Product Management with CJWinter and its manufacturing divisions. Lib is a member and has served on governing boards for the Society of Automotive Engineers, The American Society of Mechanical Engineers, and Precision Machine Products Association.